Do Manual Handling Operations Regulations Cover Equipment?
- Carey
- Jun 18, 2024
- 2 min read
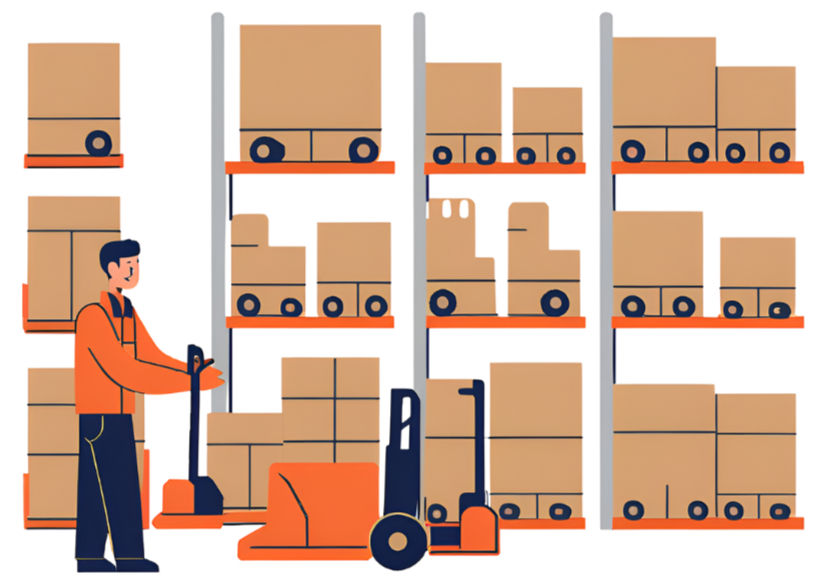
In the world of workplace safety, understanding the scope of regulations is crucial for both employers and employees. One common question that arises is whether the Manual Handling Operations Regulations (MHOR) cover equipment. This topic is particularly relevant to those who rely on equipment for lifting, carrying, or transporting goods as part of their daily tasks.
Understanding MHOR
The Manual Handling Operations Regulations 1992 (MHOR) are designed to reduce the risk of injury from manual handling activities in the workplace. These regulations emphasise the need for employers to conduct risk assessments and implement measures to minimise the risks associated with manual handling tasks. The primary focus of MHOR is on activities that involve lifting, lowering, pushing, pulling, or carrying by human effort.
Equipment and MHOR
While MHOR is primarily concerned with manual handling by employees, the use of equipment is not excluded from its considerations. Equipment that assists with manual handling tasks, such as trolleys, pallet trucks, and lifting devices, plays a crucial role in reducing the risk of injury. Under MHOR, employers are encouraged to provide appropriate equipment to minimise manual handling risks and ensure that such equipment is well-maintained and used correctly.
Employers have to ensure that any equipment used for manual handling is suitable for the task and does not introduce additional hazards. This includes regular maintenance and inspections to ensure the equipment remains in safe working condition.
Training employees on the proper use of manual handling equipment is also a critical component of compliance with MHOR.
Practical Steps for Compliance
To comply with MHOR and ensure a safe working environment, employers should:
Conduct Thorough Risk Assessments: Identify tasks that involve manual handling and assess the risks. Consider the use of equipment to reduce these risks where possible.
Provide Suitable Equipment: Ensure that appropriate manual handling equipment is available and that it is suitable for the tasks being performed.
Maintain and Inspect Equipment: Regularly inspect and maintain equipment to ensure it is in good working order and does not pose a safety risk.
Train Employees: Provide comprehensive training on safe manual handling practices and the correct use of equipment.
In summary, while the Manual Handling Operations Regulations primarily address manual handling by employees, they also encompass the use of equipment designed to assist with these tasks. Employers must ensure that such equipment is suitable, and well-maintained, and that employees are trained in its proper use. By doing so, they can significantly reduce the risk of injury and promote a safer working environment.
For more detailed information and guidance on manual handling, visit Nationwide Handling’s blog or check out our services page to see how we can help maintain your equipment. We are committed to helping you create a safer and more efficient workplace.
This information is specific to the UK market, where the Manual Handling Operations Regulations 1992 (MHOR) apply. For more detailed guidelines and resources, the Health and Safety Executive (HSE) provides comprehensive advice and requirements for compliance within the UK.
コメント